As a follow up design to the basic half bridge 555 timer IC based PWM shaped sine wave inverter circuit I came up with a second version that is a full bridge circuit intended for use at the 170 and 340 volt DC voltage levels needed for doing direct DC to 120 or 240 volt AC power conversion at line level voltages.
The overall principal of how the PWM shaped sine wave is produced in this circuit is the same as in the basic half bridge circuit but in this application the voltage feedback is not needed. The other change change is that two IRF2110 driver IC’s are used and are working in their normal high side/low side gate driver configuration.
Due to the overall similarity of the two circuits in both function and theory of operation I will not go into detail on this one being that the 555 half bridge sine wave inverter write up already gives a reasonable theory of operation relating to the components used in this circuit.
The concept behind this circuit and its intended applications is to use the existing step up and power regulation systems found in common cheap off the shelf modified sine wave inverters as the source for the regulated 170 or 340 volt DC power but make it possible to have a PWM shaped sine wave output by replacing the original modified sine wave output stage with this circuit. A second application would be for producing AC sine wave power from modified alternators or other home brew alternative energy DC based generator systems that have their own voltage regulation systems.
Power Switching devices.
For the switching devices I recommend they have a 2x working voltage rating over the maximum DC voltage where ever possible and a 4x peak current capacity rating over what the unit is intended to have as a peak load as well.
C17 and L1a/L1b.
On the output there are two iron core type inductors shown that work with C17 as the final stage filter to dampen the 30 KHz carrier frequency on the 50 or 60 Hz sine wave. For these two inductors their values and design have to be matched to the power levels that this circuit is working at so there is no exact number or size I can give you size wise. The best rough rule would be to use a pair of common laminated iron transformer cores with approximately 10 - 30 turns of wire of a size adequate to carry the peak working amperage expected from this circuit.
Ideally this inductor pair can be calculated to an exact value along with C17 to provide the best possible filtering but unfortunately numbers on paper do not tell you what your available parts actually have as real applied working values. However if a 1 uf poly capacitor was used for C17 it would exhibit roughly 5.6 ohms of impedance at 30 KHz and around 2650 ohms of impedance at 60 Hz. A suggested inductance value for the L1a and L1b inductors would be around 1.5 – 3 uh. At 30 KHz a 3 uH inductor would provide roughly 560 ohms of impedance but at 60 Hz it would only produce around 1 ohm. With those two approximate values you would be getting roughly a 100:1 attenuation of the 30 KHz carrier frequency on the output.
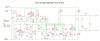
Click on thumbnail for full size view.
The overall principal of how the PWM shaped sine wave is produced in this circuit is the same as in the basic half bridge circuit but in this application the voltage feedback is not needed. The other change change is that two IRF2110 driver IC’s are used and are working in their normal high side/low side gate driver configuration.
Due to the overall similarity of the two circuits in both function and theory of operation I will not go into detail on this one being that the 555 half bridge sine wave inverter write up already gives a reasonable theory of operation relating to the components used in this circuit.
The concept behind this circuit and its intended applications is to use the existing step up and power regulation systems found in common cheap off the shelf modified sine wave inverters as the source for the regulated 170 or 340 volt DC power but make it possible to have a PWM shaped sine wave output by replacing the original modified sine wave output stage with this circuit. A second application would be for producing AC sine wave power from modified alternators or other home brew alternative energy DC based generator systems that have their own voltage regulation systems.
Power Switching devices.
For the switching devices I recommend they have a 2x working voltage rating over the maximum DC voltage where ever possible and a 4x peak current capacity rating over what the unit is intended to have as a peak load as well.
C17 and L1a/L1b.
On the output there are two iron core type inductors shown that work with C17 as the final stage filter to dampen the 30 KHz carrier frequency on the 50 or 60 Hz sine wave. For these two inductors their values and design have to be matched to the power levels that this circuit is working at so there is no exact number or size I can give you size wise. The best rough rule would be to use a pair of common laminated iron transformer cores with approximately 10 - 30 turns of wire of a size adequate to carry the peak working amperage expected from this circuit.
Ideally this inductor pair can be calculated to an exact value along with C17 to provide the best possible filtering but unfortunately numbers on paper do not tell you what your available parts actually have as real applied working values. However if a 1 uf poly capacitor was used for C17 it would exhibit roughly 5.6 ohms of impedance at 30 KHz and around 2650 ohms of impedance at 60 Hz. A suggested inductance value for the L1a and L1b inductors would be around 1.5 – 3 uh. At 30 KHz a 3 uH inductor would provide roughly 560 ohms of impedance but at 60 Hz it would only produce around 1 ohm. With those two approximate values you would be getting roughly a 100:1 attenuation of the 30 KHz carrier frequency on the output.
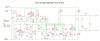
Click on thumbnail for full size view.
Last edited: