Mosaic
Well-Known Member
Hi folks ,note this graph with a pulsed voltage (yellow) vs current (blue). The line inductance is clearly not saturated as the current is still rising by the time the voltage pulse stops.
Is there any way to derive line impedance (deltaV/deltaI) from this data? Or do I need to wait until the current saturates?
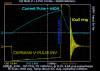
Is there any way to derive line impedance (deltaV/deltaI) from this data? Or do I need to wait until the current saturates?
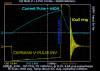