Long post, but I underlined the main issues I would like to get help with.
I've been working on an analog DC-motor simulator circuit. I'm not sure why, maby it could be usefull for automation students etc.
The system is supposed to work as follows:
Input for the circuit is analog voltage from 0 to 5V. Virtual ground is at 2.5V and it represent 0 volts across the motor. 5V represents max positive voltage across motor, and 0V is max negative voltage across motor armature.
The simulator circuit creates analog signal 0...5V representing the speed of the motor. 2.5V (virtual ground) is zero speed. Voltages below 2.5V are negative speed and above 2.5V positive speed. The circuit also simulates armature current (torque).
The goal is to simulate quadrature encoder also. I have a circuit that does that by taking two inputs; The speed as a frequency (clock signal) and direction information as logic signal.
Between the analog speed information and the quadrature encoder circuit I need a voltage to frequency converter. It does not have to be perfect. The problem I have is how to deal with "near zero speed" situation.. which is analog voltages at ~2.5V. The circuit should have small deadband around the virtual ground.
I have a signal conditioner for V to F converter. The signal conditioner takse the -2.5V...+2.5V (relative to virtual ground) speed information and rectifies it to magnitude information 0V...5V (relative to "real ground") and logic direction signal. I would like to get frequency range near 0Hz to 500kHz over the 0V...5V signal.
So, I need ideas for the voltage to frequency converter? I have found some ICs like AD654 should I just go with that? Could I build one using basic op-amps or 555 etc.?
Any ideas creating small hysteresis/deadband around 0 speed (virtual ground)? Any other comments, ideas, improvements.. or possible mistakes in my design or motor transfer function?
In the attached graph you can see:
- Input voltage to motor (blue)
- Simulated motor speed (green)
- Simulated quadrature decoder output (the digital signals at bottom)
- Rectified speed magnitude signal 0V...5V (red)
- Digital motor direction information
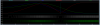
I've been working on an analog DC-motor simulator circuit. I'm not sure why, maby it could be usefull for automation students etc.
The system is supposed to work as follows:
Input for the circuit is analog voltage from 0 to 5V. Virtual ground is at 2.5V and it represent 0 volts across the motor. 5V represents max positive voltage across motor, and 0V is max negative voltage across motor armature.
The simulator circuit creates analog signal 0...5V representing the speed of the motor. 2.5V (virtual ground) is zero speed. Voltages below 2.5V are negative speed and above 2.5V positive speed. The circuit also simulates armature current (torque).
The goal is to simulate quadrature encoder also. I have a circuit that does that by taking two inputs; The speed as a frequency (clock signal) and direction information as logic signal.
Between the analog speed information and the quadrature encoder circuit I need a voltage to frequency converter. It does not have to be perfect. The problem I have is how to deal with "near zero speed" situation.. which is analog voltages at ~2.5V. The circuit should have small deadband around the virtual ground.
I have a signal conditioner for V to F converter. The signal conditioner takse the -2.5V...+2.5V (relative to virtual ground) speed information and rectifies it to magnitude information 0V...5V (relative to "real ground") and logic direction signal. I would like to get frequency range near 0Hz to 500kHz over the 0V...5V signal.
So, I need ideas for the voltage to frequency converter? I have found some ICs like AD654 should I just go with that? Could I build one using basic op-amps or 555 etc.?
Any ideas creating small hysteresis/deadband around 0 speed (virtual ground)? Any other comments, ideas, improvements.. or possible mistakes in my design or motor transfer function?
In the attached graph you can see:
- Input voltage to motor (blue)
- Simulated motor speed (green)
- Simulated quadrature decoder output (the digital signals at bottom)
- Rectified speed magnitude signal 0V...5V (red)
- Digital motor direction information
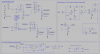
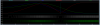
Last edited: