painstream
New Member
Having trouble wrapping my head around this..
So lets say we have two voltage sources, and a dc fan, and we want a user to control the fan speed manually. Lets say one voltage source is coming from a micro controller and the other in independent.
Voltage Sources: 12v and 5v
First of all we do not want the fan to drop before its rated stall current of 5 volts and we want it to use a max rated voltage 12 volt.
We are using a pot to control the current to a npn transistor. Attached is a working schematic that does exactly what we want. I'm having trouble understanding the math involved with the voltage divider on the 5v side. Calculating the pot is confusing me. If I put a 10k pot the fan will not start until I turn the pot a bit(current is to low) to the base of the transistor. Can someone help me explain the math?
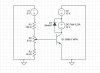
So lets say we have two voltage sources, and a dc fan, and we want a user to control the fan speed manually. Lets say one voltage source is coming from a micro controller and the other in independent.
Voltage Sources: 12v and 5v
First of all we do not want the fan to drop before its rated stall current of 5 volts and we want it to use a max rated voltage 12 volt.
We are using a pot to control the current to a npn transistor. Attached is a working schematic that does exactly what we want. I'm having trouble understanding the math involved with the voltage divider on the 5v side. Calculating the pot is confusing me. If I put a 10k pot the fan will not start until I turn the pot a bit(current is to low) to the base of the transistor. Can someone help me explain the math?
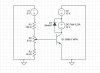