JJ2430
Member
I received my new uC and tested connections on breadboard with suggestions provided by Mike. So far everything work as it should and the circuit is very stable, even on uC boot-up: GPIO 5 is indeed providing high impedance so resistor is no longer needed between GPIO and INA. The solenoid's response is fast and without glitch. For now the circuit is currently running on a 12VDC psu and the uC uses Li-Ion 5V. I will perform further tests and assemble the final PCB with solder. I also received the Lipo 6A. Tested it to verify voltage of each individual cell and total. The battery looks in proper shape at 3.81V each cell for a total of 15.24V. This is the usual "resting" charge and corresponds to about 35% of charge. The intelligent charger is on the way. Will give the battery 2 to 3 cycles to "break it", as recommended, before putting it under more serious use. I'm also waiting for the balance protection pcb and buck converter. I ordered a Lipo low voltage monitor/buzzer that I will install in the circuit and adjust to 3.7V per cell in order to avoid undercharge.
I linked a video and attached pictures of the latest developments.
Previous connections before Mike's latest recommendations:
Latest connections:
Video:
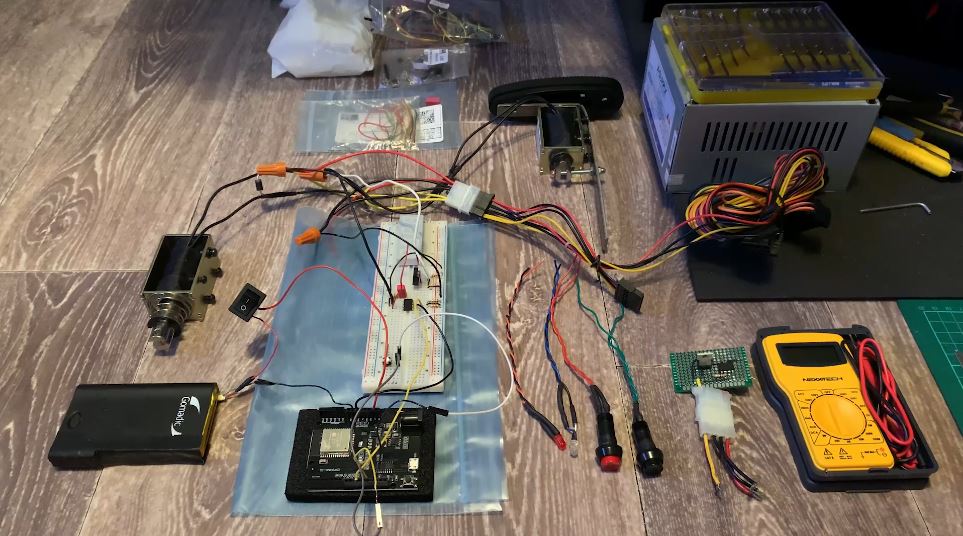
I will implement the Lipo once the protection pcb and buck converter are here. I will follow Rj's recommendation of unplugging and removing battery from rig for charging since the charger monitors balance as well. I've been reading a lot on Lipo technology over the last days and the precautions to take to enhance battery life for one, and also to prevent hazards such like explosions and fire. It is preferable to charge the battery in a safe environment and not tethered to the system it is powering.
I will connect the Lipo the same way as depicted in the image below. The pcb will be permanently connected to the system and the battery removed for each charging cycle.
I linked a video and attached pictures of the latest developments.
Previous connections before Mike's latest recommendations:
Latest connections:
Video:
I will implement the Lipo once the protection pcb and buck converter are here. I will follow Rj's recommendation of unplugging and removing battery from rig for charging since the charger monitors balance as well. I've been reading a lot on Lipo technology over the last days and the precautions to take to enhance battery life for one, and also to prevent hazards such like explosions and fire. It is preferable to charge the battery in a safe environment and not tethered to the system it is powering.
I will connect the Lipo the same way as depicted in the image below. The pcb will be permanently connected to the system and the battery removed for each charging cycle.