Hi everyone,
I just came across this site while doing some research on the circuit I am trying to build and found it to be full of information with lots of interesting projects.
I am trying to build an under voltage detection circuit for a 12V car battery. The vehicle this would go into uses several pieces of equipment and recently people have been forgetting to turn off the equipment when they are finished, and thus the battery is dead the next day.
I want to build the circuit using an op amp as my voltage comparator and have attached a picture of what I have so far. I would like the circuit to turn off everything when the voltage reaches about 12.2V. I have attempted to do that using a 6.2 zenor diode as my reference voltage and a voltage divider for my variable voltage.
I also wanted to add in a reset switch that someone would need to push in order to turn the system back on, but I am not sure how to implement that yet.
There is still several issue with this setup so far I think with the transistor and all, but I was hoping I could get some feedback and suggestions on what I have so far.
Sorry for the long post.
Thanks for your help!
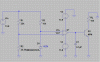
I just came across this site while doing some research on the circuit I am trying to build and found it to be full of information with lots of interesting projects.
I am trying to build an under voltage detection circuit for a 12V car battery. The vehicle this would go into uses several pieces of equipment and recently people have been forgetting to turn off the equipment when they are finished, and thus the battery is dead the next day.
I want to build the circuit using an op amp as my voltage comparator and have attached a picture of what I have so far. I would like the circuit to turn off everything when the voltage reaches about 12.2V. I have attempted to do that using a 6.2 zenor diode as my reference voltage and a voltage divider for my variable voltage.
I also wanted to add in a reset switch that someone would need to push in order to turn the system back on, but I am not sure how to implement that yet.
There is still several issue with this setup so far I think with the transistor and all, but I was hoping I could get some feedback and suggestions on what I have so far.
Sorry for the long post.
Thanks for your help!
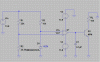