edmond_chan85
New Member
Hi,
I had built a boost converter with a constant 24V output voltage from an input voltage ranging from 6-23V with a power rating of 100W. The converter is operating at 20kHz. I am able to boost up the voltage until 24V. But the problem is that my converter's efficiency is quite low (around 60-70%) and I am suspecting the losses in switch. I am using IRF540N power MOSFET.
Weird thing happen when I measure the voltage across and current through IRF540N. The current and the voltage waveform are in phase!!which means that when my switch is off, current passes through. when my switch is on, no current flow. But my converter is still performing well as it is able to step up my input voltage to 24V output voltage.
Any ideas??Please help me...My target is about 90% efficiency..
The 1st attachment is my diode waveform. The 2nd attachment is my switch waveform.
p/s: sorry for my poor english and can i post figure without using attachment?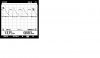
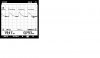
I had built a boost converter with a constant 24V output voltage from an input voltage ranging from 6-23V with a power rating of 100W. The converter is operating at 20kHz. I am able to boost up the voltage until 24V. But the problem is that my converter's efficiency is quite low (around 60-70%) and I am suspecting the losses in switch. I am using IRF540N power MOSFET.
Weird thing happen when I measure the voltage across and current through IRF540N. The current and the voltage waveform are in phase!!which means that when my switch is off, current passes through. when my switch is on, no current flow. But my converter is still performing well as it is able to step up my input voltage to 24V output voltage.
Any ideas??Please help me...My target is about 90% efficiency..
The 1st attachment is my diode waveform. The 2nd attachment is my switch waveform.
p/s: sorry for my poor english and can i post figure without using attachment?
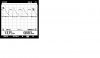
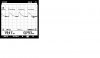
Last edited: