I have recently acquired a high frequency stabilizer which allows an AC welder to weld aluminum using TIG equipment. I am new to TIG welding but want to learn more about it and this seemed like a good way of getting into it. I have been having a tough time welding with it though. I have had some input from a welding friend and he bounces ideas off of a good tig welder but together we have had no luck. After troubleshooting all of the typical Tig type problems, I am starting to suspect the HF box, although it does appear to work well. I get a great arc from the tungsten to the material and can melt the base material just fine, and run the arc along the material. But the material does not seem to "mix" ...it seems to blow away like I am using DC but I tried another power source (welder) and it does the same thing. The HF box uses a spark gap to generate the HF. I know very little about this but the manual does suggest a spark gap of 0.007". I set it to this, and a little more and a lot less and none make a diffence. The HF at the tungsten is very strong (ie jumps quarter inch or more ) so it appears to work but the welding part does not.
Sooo, after all that, my question is this. In the large coil that the welding current flows through in the box (in and then out), there are three wires going into the coil. One comes from either side of the spark gaps and the third goes to one of the output terminals. I get no continuity on any of these wires. I have no diagram so am guessing but I would think there should be something there...? The confusing part is that I have great arcing on the output and can maintain the weld. I have labelled the wires I am referring to as A, B and C in the attached photo. I think these wires are supposed to super impose the HF on the welding current which it appears to do but thought I would throw this out there and see if anyone has any experience with this sort of thing.
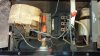
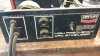
Sooo, after all that, my question is this. In the large coil that the welding current flows through in the box (in and then out), there are three wires going into the coil. One comes from either side of the spark gaps and the third goes to one of the output terminals. I get no continuity on any of these wires. I have no diagram so am guessing but I would think there should be something there...? The confusing part is that I have great arcing on the output and can maintain the weld. I have labelled the wires I am referring to as A, B and C in the attached photo. I think these wires are supposed to super impose the HF on the welding current which it appears to do but thought I would throw this out there and see if anyone has any experience with this sort of thing.
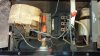
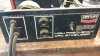