Here is the external watch-crystal oscillator I am using:
It is built on strip board (3 holes per pad) for plugging into my breadboard. The circuit is here: https://microchip.wikidot.com/8bit:t1secosc
Frequency was a little high with 8.2 pF load capacitors, so I increased them to 10.4 pF each. With my scope and counter (Racal-Dana #1992), the frequency is now about right. When I use it to clock TMR1 and capture known frequencies, namely 60 Hz and 1 kHz, the 2 or 3 significant figure results are right on, but the crystal is supposedly accurate to 20 ppm or so.
If you put any load on the crystal, such as with the scope, you change its frequency. Is there an accepted and relatively easy way to determine its frequency more precisely in the MCU circuit?
John
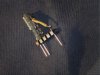
It is built on strip board (3 holes per pad) for plugging into my breadboard. The circuit is here: https://microchip.wikidot.com/8bit:t1secosc
Frequency was a little high with 8.2 pF load capacitors, so I increased them to 10.4 pF each. With my scope and counter (Racal-Dana #1992), the frequency is now about right. When I use it to clock TMR1 and capture known frequencies, namely 60 Hz and 1 kHz, the 2 or 3 significant figure results are right on, but the crystal is supposedly accurate to 20 ppm or so.
If you put any load on the crystal, such as with the scope, you change its frequency. Is there an accepted and relatively easy way to determine its frequency more precisely in the MCU circuit?
John